Medical Device GMP...
Information | Understanding | Best Practice.
Medical Device GMP Training requirements are detailed in the US FDA CFR’s, the European Medical Device Regulations (MDR’s), by Health Canada, by ANZTPA (Australia, New Zealand, Therapeutic Products Agency), … and many other international regulatory bodies.Introduction.
When considering training, first we need to define the following terms: “Skills”, “Knowledge”, “Attitudes”.A “skill” is a developed aptitude or ability in a particular intellectual or physical field.
“Knowledge” is information which is specific to a subject, enabling you to understand a subject to an acceptable level.
“Attitude” is an internal state which affects your choice of action towards some objects, persons or events.
FDA GMP Training requirements …
GMP demands training at the induction stage for all new employees who could affect the quality or efficacy of the product. Training then needs to progress with the employee as their time and career progresses within the organization.GMP similarly demands training for contractors working on site, where they could impact the product.
GMP refresher training also needs to be considered, defined, documented and implemented.
Per CFR 820.25:
(a) General. Each manufacturer shall have sufficient personnel with the necessary education, background, training, and experience to assure that all activities required by this part are correctly performed.
(b) Training. Each manufacturer shall establish procedures for identifying training needs and ensure that all personnel are trained to adequately perform their assigned responsibilities. Training shall be documented.
(1) As part of their training, personnel shall be made aware of device defects which may occur from the improper performance of their specific jobs.
(2) Personnel who perform verification and validation activities shall be made aware of defects and errors that may be encountered as part of their job functions.
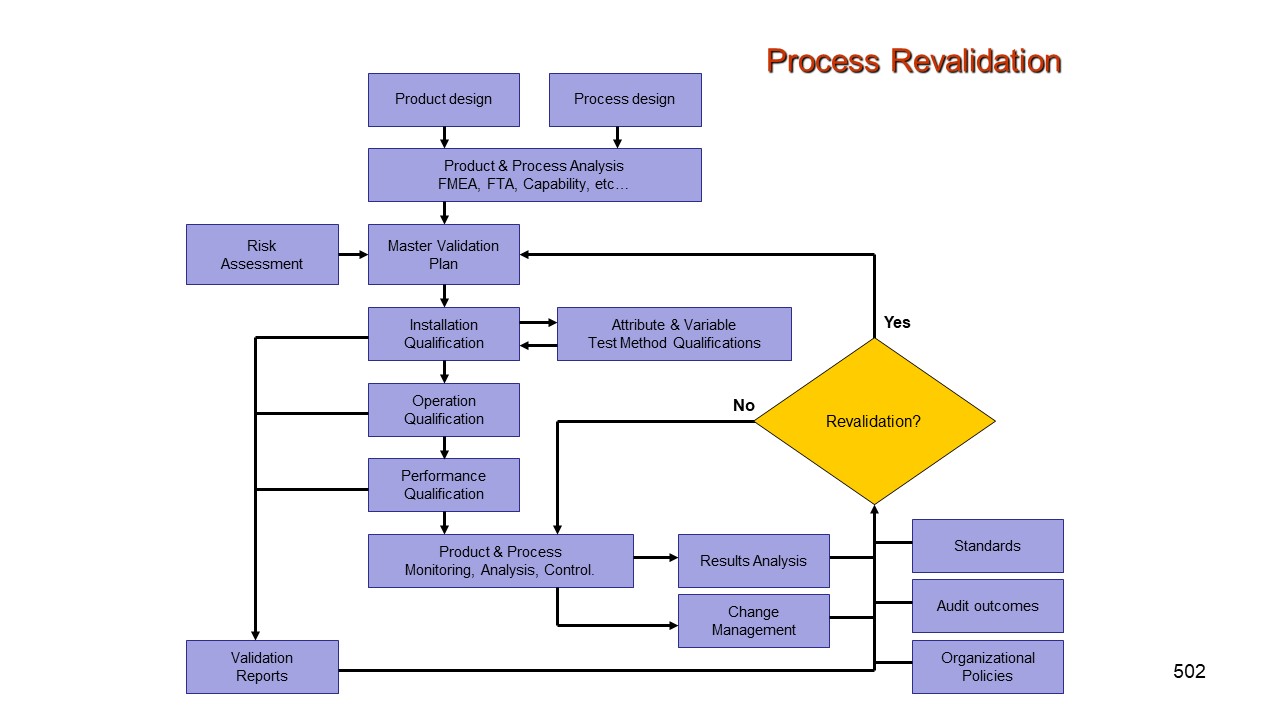
Validation. Classification. Regulation. Requirements. Current best practices.
FDA cGMP’s. EU MDR’s / MDD’s.
Etc. Etc. …
Information | Understanding | Best Practice >>>
To effectively implement GMP Training you need to understand:
What are the driving forces, behind the need to provide the training.What is the organization’s training policy.
What are the relevant GMP requirements for training.
The various types of training that may be utilized.
The training methods to be employed.
The need to develop a plan for the training.
Method of training assessment to be applied and
What is the policy towards training records.
Per the FDA (Medical Devices):
Manufacturers must establish and follow quality systems to help ensure that their products consistently meet applicable requirements and specifications. The quality systems for FDA-regulated products (food, drugs, biologics, and devices) are known as current good manufacturing practices (CGMP’s). CGMP requirements for medical devices are detailed in part 820 of the FDA CFR’s (21 CFR part 820).Title 21 – FDA, Chapter 1, Subchapter H, Medical Devices.
Current good manufacturing practice (CGMP) requirements are set out in the Quality System (QS) regulation. The requirements govern the methods used in, the facilities and controls used for, the design, manufacture, packaging, labeling, storage, installation, and servicing of all finished devices intended for human use. The requirements are intended to ensure that finished devices will be safe and effective and otherwise in compliance with the Federal Food, Drug, and Cosmetic Act (the act).The QS regulation embraces the same “umbrella” approach to the CGMP regulation that was the underpinning of the original CGMP regulation. Because the regulation must apply to so many different types of devices, the regulation does not prescribe in detail how a manufacturer must produce a specific device. Rather, the regulation provides the framework that all manufacturers must follow by requiring that manufacturers develop and follow procedures and fill in the details that are appropriate to a given device according to the current state-of-the-art manufacturing for that specific device.
Manufacturers should use good judgment when developing their quality system and apply those sections of the Quality System (QS) regulation that are applicable to their specific products and operations, (21 CFR 820.5 of the QS regulation).
The QS regulation applies to finished device manufacturers who intend to commercially distribute medical devices. A finished device is defined in 21 CFR 820.3(l) as any device or accessory to any device that is suitable for use or capable of functioning, whether or not it is packaged, labeled, or sterilized.
Per the FDA (2018), in the publication titled “Harmonizing and Modernizing Regulation of Medical Device Quality Systems”, proposed rule change:
FDA intends to harmonize and modernize the Quality System regulation for medical devices. The revisions will supplant the existing requirements with the specifications of an international consensus standard for medical device manufacture, ISO 13485:2016. The revisions are intended to reduce compliance and recordkeeping burdens on device manufacturers by harmonizing domestic and international requirements. The revisions will also modernize the regulation.
The ISO 13485 Standard: Medical Devices — Quality Management Systems — Requirements for regulatory purposes,
Is the International Standard for quality management systems for the medical devices sector.ISO Medical Device GMP Training requirements e.g. ISO 13485 …
“Personnel performing work affecting product quality shall be competent on the basis of appropriate education, training, skills and experience.”Per the ISO standard the organization shall:
Determine the necessary competence for personnel performing work affecting product quality.
Provide training or take other actions to satisfy these needs.
Evaluate the effectiveness of the actions taken.
Ensure that its personnel are aware of the relevance and importance of their activities and how they contribute to the achievement of the quality objectives, and
Maintain appropriate records of education, training, skills and experience.

Medical Device:
- Validation. Classification. Regulation. Requirements. Current best practices.
- FDA cGMP’s. EU MDR’s / MDD’s.
- FDA Medical Device Regulation.
- FDA Medical Device Classification.
- EU Medical Device Regulation and Classification (per MDD’s).
- European Medical Device Regulations (MDR’s).
- Current Good Manufacturing Practices. QSR’s. General requirements of the QSR’s.
- Quality System requirements to maintain compliant Validations.
- Medical Device Process Validation. IQ. OQ. PQ’s.
- Medical Device Software Validation.
- Medical Device Design Validation.
- Electronic Signature, Electronic Records.
- Life Cycle Approach to Validation.
- Risk Identification. Documentation. DHR’s. DMR’s.
- Etc. Etc. …
- Information | Understanding | Best Practice >>>
US FDA Quality System Regulation. Current Good Manufacturing Practice Regulations – Medical Device
US FDA Current Good Manufacturing Practice Regulations – Pharmaceutical